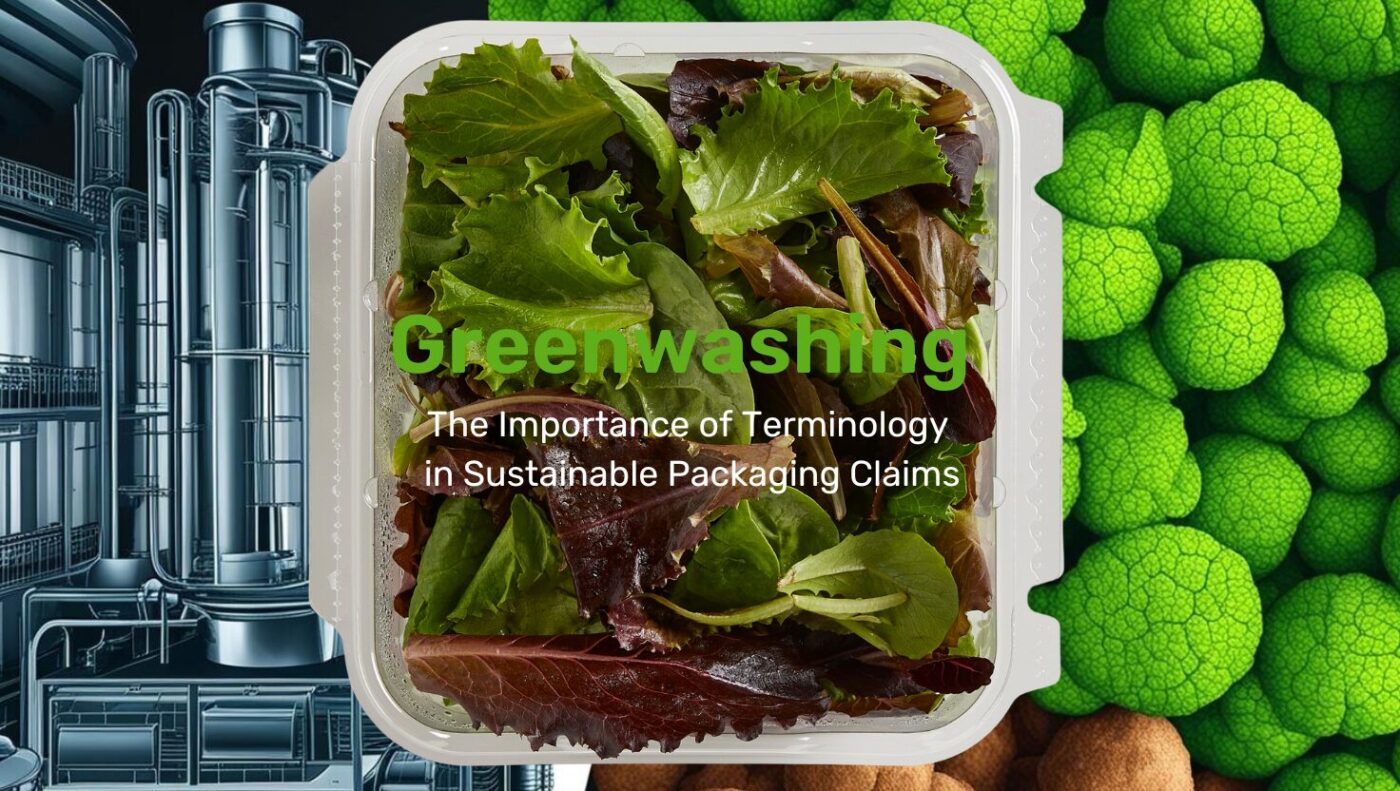
Understanding the Language of Sustainability As the push for sustainable packaging grows,…
Today, more and more health care product manufacturing, assembly, and packaging processes are using automation to ensure highly efficient, smooth operations.
This shift toward automation is already allowing for a range of benefits, and is expected to continue rising in popularity. Health care automation allows for higher speeds of production, as well as enhanced safety since managers are granted greater control over all processes.
Plus, monitoring the parameters of equipment performance allows manufacturers to rectify issues immediately, ensuring consistently high quality while cutting down on maintenance needs and downtime.
Streamlined traceability is another key advantage, helping brands maintain their reputations as trustworthy leaders in the industry.
Thermoformed plastic packaging trays often play a key role in health care manufacturing, assembly, and packaging processes.
When thermoformed plastic packaging trays are designed to align with clients’ specific needs, the trays can then be integrated seamlessly into a facility’s packaging automation equipment.
Thermoformed plastic packaging trays provide great design flexibility and can be tailored to clients’ unique requirements. These versatile trays can also be custom designed to allow for enhanced brand visibility and aesthetic value. They also provide reliable protection during potentially damaging assembly and packaging processes.
When designing thermoformed trays to integrate with a health care operation’s automated system, a number of key factors should be considered.
When creating a thermoformed plastic packaging tray, it’s important to first determine the orientation and configuration of the product in the tray.
Orientation is usually horizontal or vertical; configuration, on the other hand, can be significantly more complex.
Deciding on the configuration and orientation of a tray requires expert consultation, thorough engineering analysis, and careful weighing of the pros and cons of each option.
Downstream processes — such as stacking and cartoning — and their effects must also be taken into account.
In many automated systems, it’s necessary to match the pitch of the end-of-arm tooling and maintain dimensional consistency.
These actions are critical for ensuring maximum system efficiency and require in-depth knowledge of the specifications of the automation system.
Dimensional consistency is particularly important, as the large footprint of most thermoformed trays can present unique challenges in minimizing variation.
To help ensure dimensional consistency, consider the different forces a thermoformed tray may encounter during manufacturing and packaging.
Also, conduct a step-by-step failure mode analysis of the automated processes to allow for easier material selection.
This will also help in deciding whether to include robust design features — such as ribs and chamfers — or specific tooling attributes designed to achieve ideal material distribution, which may involve allowing for greater thickness in vulnerable areas.
Plastic Ingenuity has the expertise and experience necessary to ensure the successful design and implementation of thermoformed trays for your automated health care packaging needs, no matter how complex.
Committed to quality in everything we do, our team works closely with all third parties to guarantee seamless integration of our trays into clients’ systems.
To read up on other important design considerations, download our free eBook, “Development Guide for Automated Healthcare Packaging.” Or, to speak with one of our experts about your specific medical device or pharmaceutical project, reach out to the team today.