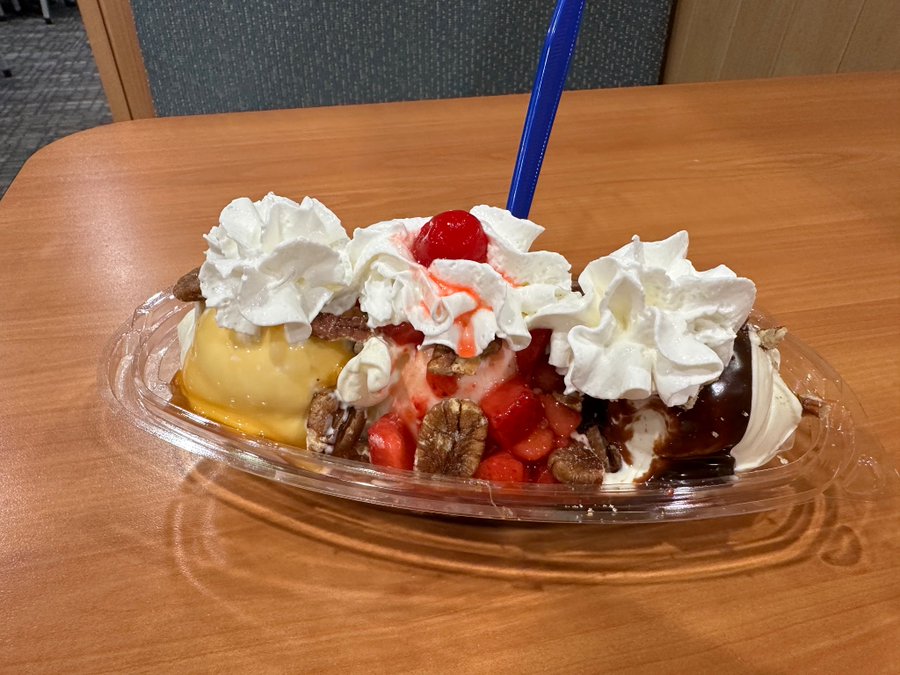
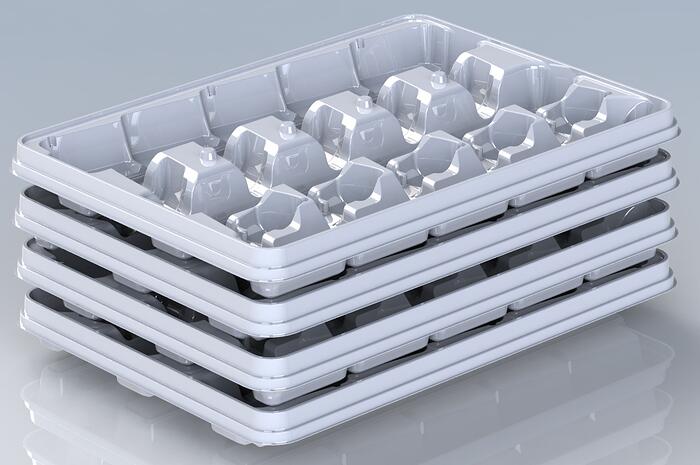
The Challenge
Assessing the Damage
Merit Medical Systems, Inc., a manufacturer of single-use medical devices for interventional and diagnostic procedures, turned to Plastic Ingenuity to design a solution to eliminate shipping damage, decrease material waste, and reduce packaging costs.
Merit’s inflation devices for angioplasty procedures consist of multiple configurations, including a range of sizes, lengths of tubing, and various gauges. Unfortunately, the delicate gauge often incurred damage during global distribution from vibration, shock, and environmental stresses. Due to the challenges Merit faced passing validation, the product line launched using single-device, single-use packaging consisting of a PETG tray and insert, Tyvek lid, carton, and heavy duty corrugate. As the product line expanded, this stop-gap solution led to increasing material waste, labor, warehousing, and distribution.
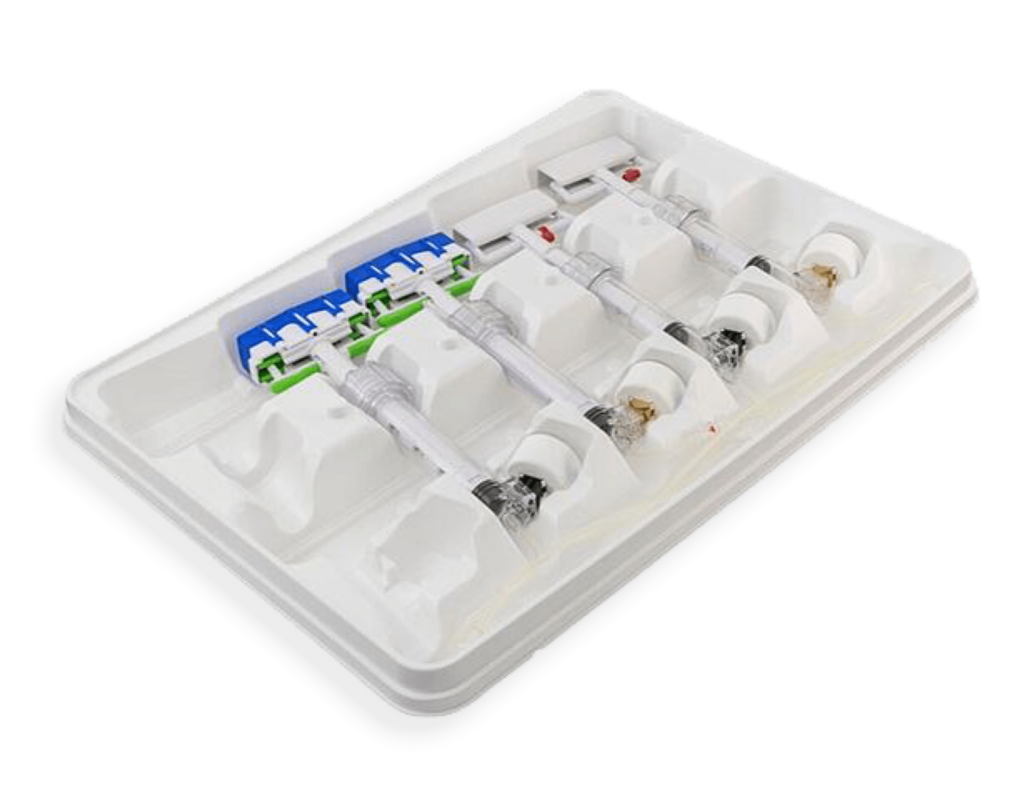
The Process
Material Innovation + Design Excellence
Material selection is critical for shipping trays. Commonly used materials like HIPS are rigid and unforgiving. To develop a solution capable of delivering the protection required, we leveraged Eastalite™ copolyester, a novel foamed PETG material. As the first commercial Eastalite™ application on the market, this material provides a lower density than traditional rigid materials, greater abrasion resistance, and improved shock absorption and impact strength.
After selecting the material, we designed a bulk universal tray capable of accommodating all devices, sizes, and configurations with one tray. The universal cavity design prevents device vibration and movement, improving product protection with zero rejects in the bulk pack solution.
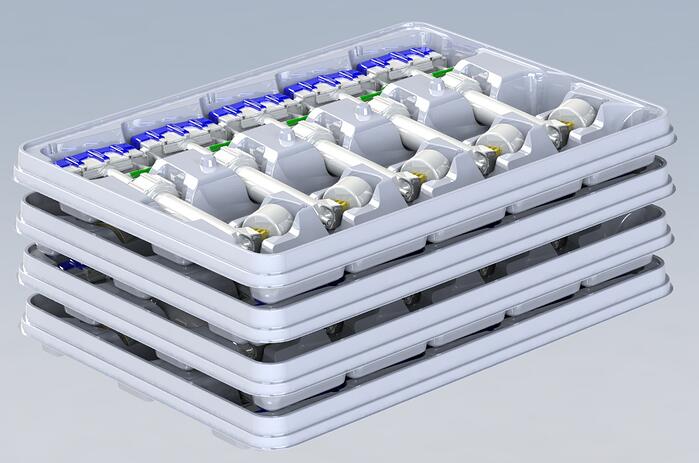
The Solution
Exceeding Expectations
Our universal transport tray design innovation created a single packaging component that works with multiple devices within the same product line. The design not only accommodates all devices, sizes, and configurations in one tray, but it also offers improved product protection, minimum bending to the flexible tubing, no tray-to-product contact, and reusability. This first-to-market Eastalite™ application provides cushioning to prevent damage to the delicate device while being robust enough for reuse ≥ 4x.
The solution exceeded all functional, economic, and environmental goals. With increased efficiencies, the packaging labor burden was reduced 57% and cube utilization was optimized 133% to accommodate 1,400 devices/pallet vs 600 devices/pallet.
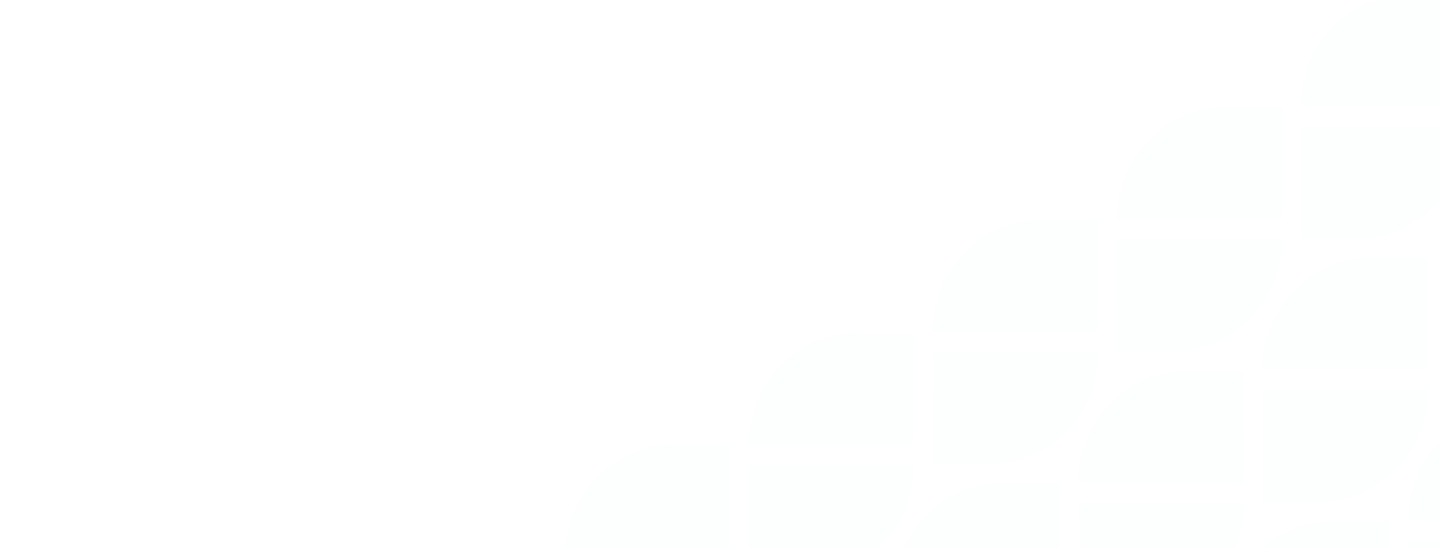
The Results
Waste Reduced, Money Saved
increase in devices per pallet
reduction in transatlantic freight costs
reduction in packaging material costs
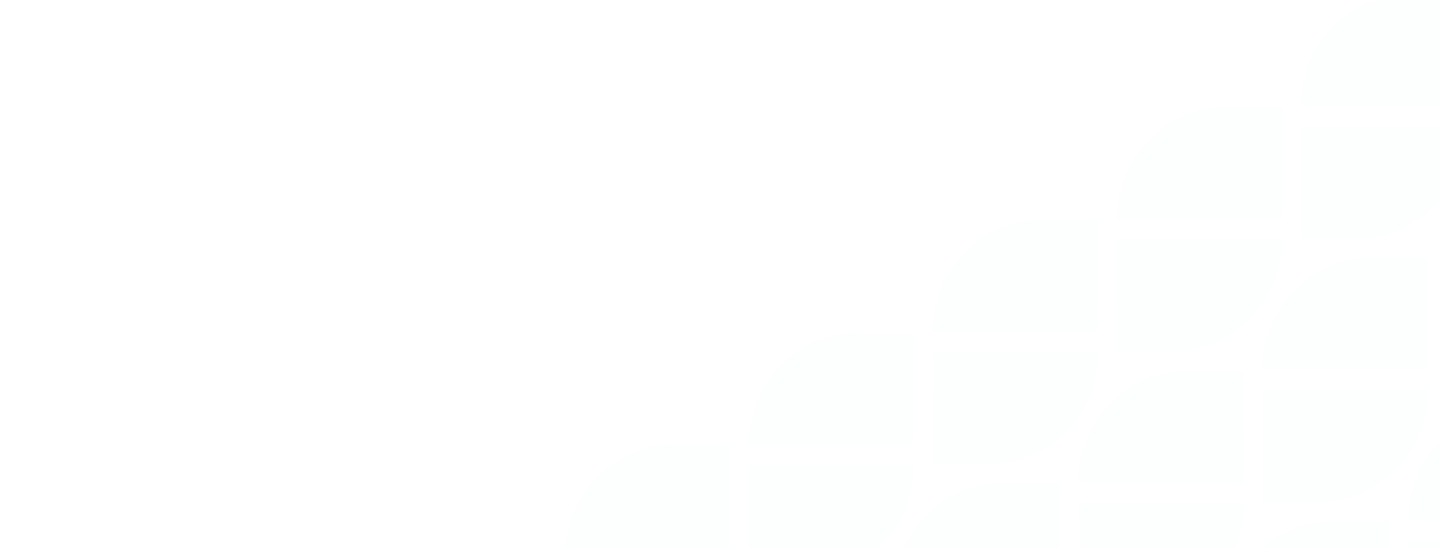