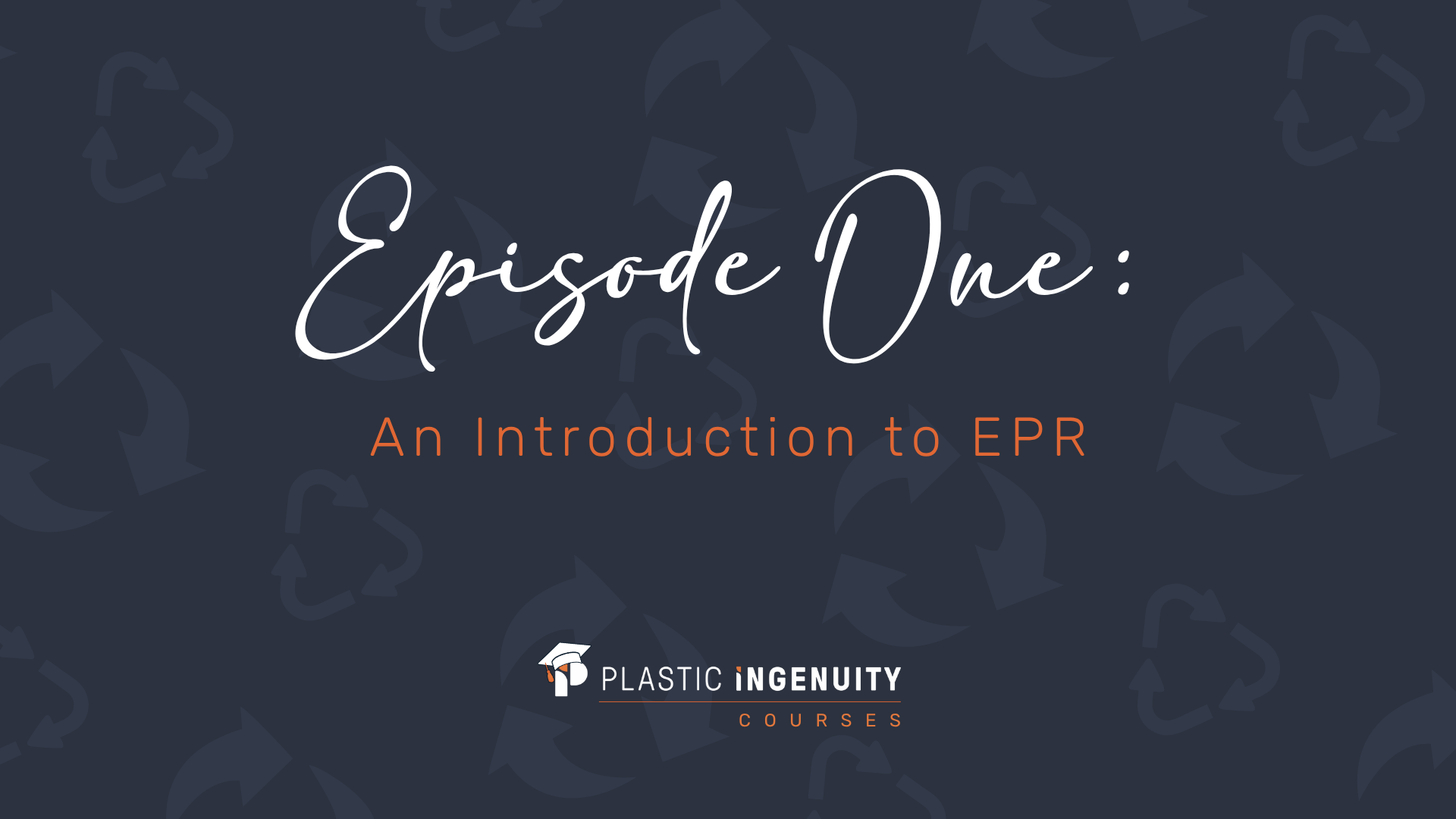
Understanding Packaging EPR: What Brands Need to Know Get up to speed…
In the recent past, the healthcare industry has experienced a seismic shift, especially in medical device manufacturing, with syringe packaging being among the most impacted areas.
Modern consumers’ rising preference for prefilled syringes is fanning the changes in syringe packaging. Today, consumers have greater access to biological therapies requiring subcutaneous injections, and most favor self-administered injections over facility-based treatment.
This has gradually skyrocketed the demand for prefilled syringes. And medical device packaging engineers must elevate their standards to satisfy the surging demand. More importantly, your packaging standards must accommodate higher fragility levels of the liquid medicine in prefilled syringes.
Knowing syringe packaging affects the quality and purity of your medicine and end-user convenience, you must get syringe packaging right the first time. Luckily, this detailed guide will tell you all you need to know about syringe packaging and the fundamental aspects you must consider to deliver optimum efficiency to the end users.
Let’s dive in.
Packaging is a critical aspect of the pharma industry, given the sensitive nature of pharmaceutical products. Pharma packaging ensures that drugs aren’t contaminated through improper product handling. It also preserves the curative qualities of medicine for as long as it stays in the package.
For prefilled syringes, the packaging is even more important as it preserves the sterility of the liquid medicine in the syringe. Prefilled syringe packaging utilizes two levels of packaging:
As a pharma manufacturer, quality prefilled syringe packaging helps you:
Ultimately, the most prominent role of prefilled syringe packaging is preserving the purity and quality of the fragile liquid medication in the prefilled syringe. This should take precedence when considering the type of packaging material for your prefilled syringes, whether you’re delivering vaccines or parenteral drugs.
Your syringe packaging should fulfill the following essential conditions:
Sterilization is a delicate and complex process when it comes to liquid pharmaceuticals. You must ensure your sterilization process doesn’t cause thermal changes to the prefilled syringe and the drug therein. There are several ways to sterilize medical devices, such as:
Most pharma manufacturers opt for the steam/air mixture sterilization method as it’s the most sustainable method of sterilizing glass syringes and EO or gamma for plastic syringe sterilization.
The steam/air mixture method utilizes a combination of pure steam and sterile filtered compressed air, which is released into a sterilizer chamber holding your prefilled syringes. Then radial fans and air baffles circulate and mix the compressed air and pure steam until the chamber reaches the desired temperature, typically 121 °C (250 °F).
Sterilization takes about 15 minutes, after which the sterilizer chamber is cooled to the unloading temperature. At this point, the entire batch of the prefilled syringes loaded in the chamber is thoroughly sterilized.
Ensure you complete your sterilization process accurately so that no bacteria contaminate the sensitive liquid drug in your prefilled syringes. More importantly, the sterilization properties must last throughout the shelf life of the prefilled syringes (2-3 years) to guarantee patient safety.
Ease of access is one of the top reasons end consumers and healthcare practitioners favor prefilled syringes. As such, your syringe packaging must facilitate fast access to the end users so they can administer or self-administer drugs swiftly, especially in emergencies.
Human factors and usability engineering is a top priority for the Food and Drug Administration (FDA). The FDA published a detailed guidance document in 2016 to help medical device manufacturers satisfy human factors and engineering standards to advance user accessibility.
The main goal is reducing or preventing use-related hazards such as:
To attain optimum product accessibility, ensure your syringe packaging fulfills the following aspects:
Understandably, your syringe packaging may need complex design features to enable ease of access. This may require you to seek thermoforming services from a top custom thermoformer like Plastic Ingenuity.
You must consider the environmental impact of your prefilled syringe packaging before, during, and after production, mainly if you use plastic syringes. For prefilled plastic syringes, you want to use thermo elastic polymers that end users can dispose of without harming the environment. Thermo elastic polymers contain Daikyo crystal zeniths that allow the syringes to be incinerated without producing residual dust.
You may also utilize rigid plastics for your medical device packaging as they can be recycled. Overall, whether you use distillate syringe packaging, syringe blister packaging, or rigid plastics, review their environmental effect. Aim at reducing your carbon footprint by sourcing syringe packaging materials that are less polluting.
An experienced and well-equipped thermoforming partner like Plastic Ingenuity will offer end-to-end solutions beyond syringe packaging. Our commitment to better healthcare helps us create innovative and scalable solutions for syringe packaging, storage, logistics, market entry, safety and compliance, and sustainability.
With Plastic Ingenuity on your side, you can bring new therapies to market as quickly and efficiently as possible. Rest assured that our solutions will swiftly take your syringe packaging business from innovation to integration to industrialization. Contact us today, and let us transform your syringe packaging business.