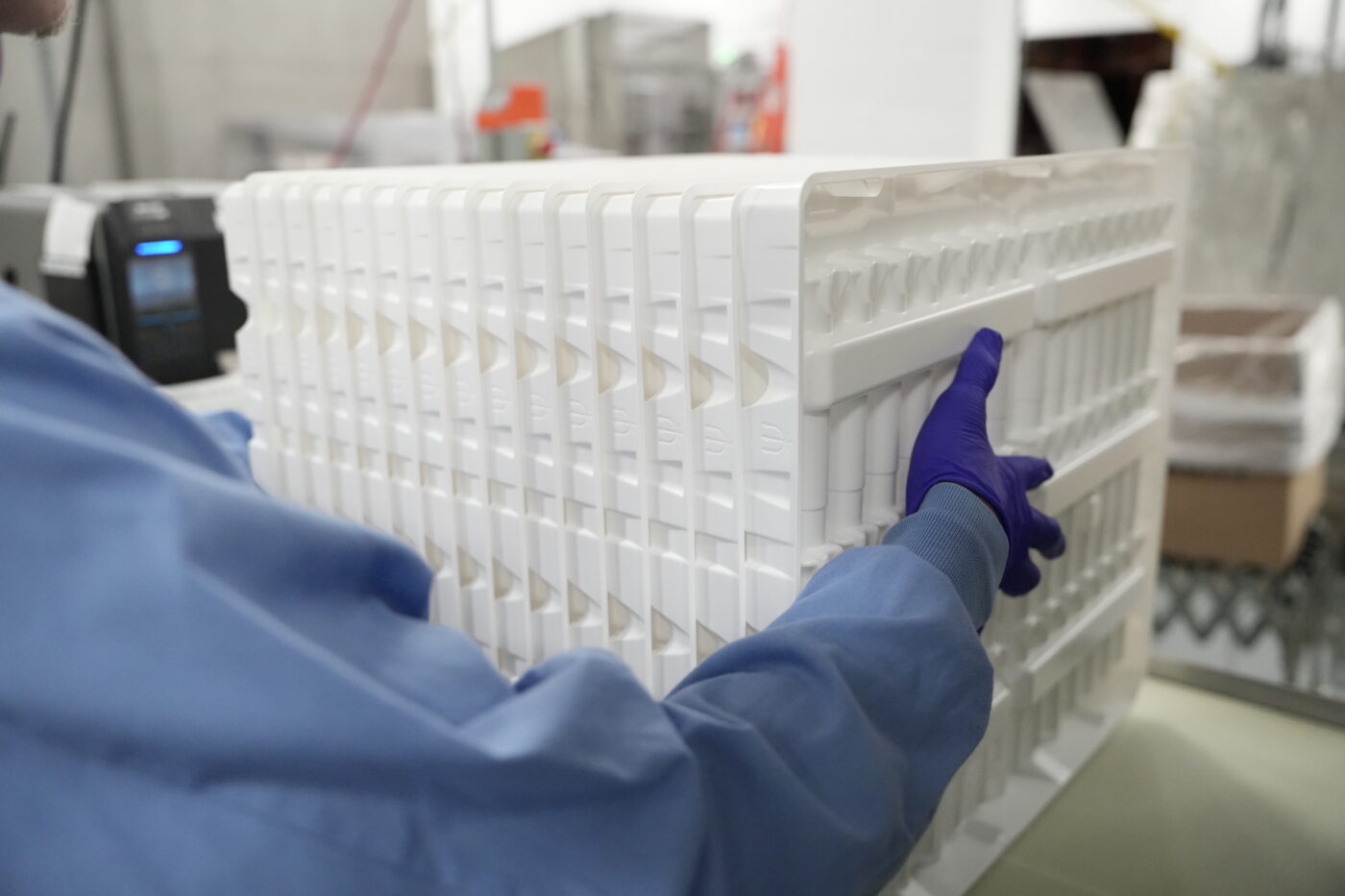
Medical devices are incredibly important in today’s world. They play a significant role in the treatment and prevention of various medical conditions. However, their effectiveness can be compromised if they are not packaged correctly. Packaging is an essential component of maintaining the integrity and shelf life of medical devices, especially during transportation and storage.
Read on to learn more about the importance of proper packaging in the medical device industry and how it can improve the shelf life of critical devices.
Understanding Shelf Life and Stability of Medical Devices
As an experienced healthcare professional, you are well aware of the critical role that medical devices play in providing effective care for patients. However, it is important to understand their shelf life and stability to ensure that you are using them safely and effectively, minimizing the risk of complications or adverse events.
Shelf Life
The shelf life of a medical device refers to the period of time during which you can store it and use it safely and effectively.
In general, medical devices are designed to meet specific performance requirements set by the International Organization for Standardization (ISO). These medical device shelf life ISO standards provide guidance on how to determine a device’s expected shelf life — often referred to as the expected lifetime — as well as the testing protocols and procedures manufacturers should follow to ensure a device’s safety and effectiveness over a certain time period.
The lifetime of devices is typically based on several factors, such as:
- Expected wear and tear
- The likelihood of material degradation or corrosion
- The potential for changes in performance over time
Additionally, the shelf life of a medical device can be affected by a range of environmental factors, including:
- Temperature
- Humidity
- Exposure to light or other sources of radiation
While medical devices have no fixed expiry requirements, you must generally submit additional data for expiration date extensions. You must also gain regulatory approval to use certain devices past their original expiration date.
Stability
The stability of a medical device refers to its ability to maintain its physical, chemical, and functional properties over time, under various environmental conditions, and after exposure to sterilization or other processing methods.
The stability of a medical device is a critical factor in ensuring its safety and efficacy. Medical devices are designed and tested to perform specific functions within a given range of conditions, such as:
- Temperature
- Humidity
- Pressure
- pH
- Light
- Gravity
Any changes in these conditions can impact the device’s stability and potentially compromise its performance, putting you and your patients at risk.
Factors Considered When Determining Shelf Life Expiration Dates
Shelf life expiration dates are vitally important to ensure medical devices are safe to use. The Food and Drug Administration (FDA) requires product labels to indicate an expiration date if a certain component is not useful past a certain date.
Therefore, medical device manufacturers consider four factors to reach a final medical device shelf life determination following FDA and ISO medical device shelf life standards.
Packaging
Through rigorous testing and analysis, packaging engineers and designers can determine how long a medical device will remain stable and effective within its packaging under various storage conditions. Thus, manufacturers can determine its expected shelf life and provide guidance to healthcare professionals on proper storage and use.
Storage Conditions
Factors such as temperature, humidity, light, and exposure to various chemicals can all influence how quickly a device will degrade or become compromised.
Therefore, manufacturers carefully monitor and complete shelf life testing of medical devices under a range of controlled storage conditions to determine the optimal conditions for maintaining the device’s stability and performance over its intended shelf life.
Manufacturing Process
The quality and consistency of the materials used and the precision of the manufacturing process itself can all impact a medical device’s stability and performance over time. The process involves various steps, including the selection of materials, product design, and packaging.
Throughout this process, manufacturers complete several quality control measures to accurately establish a shelf life expiration date, including:
- Assessing the physical and chemical properties of the materials used to determine the device’s susceptibility to degradation over time
- Considering the impact of the manufacturing environment on the product’s stability
- Conducting extensive testing throughout the manufacturing process to evaluate the device’s performance and functionality
Transportation
Finally, transportation is another critical factor that can impact a medical device’s shelf life. Medical devices may be exposed to a variety of conditions that can impact their stability and performance during transit, such as:
- Extreme temperatures
- Moisture
- Vibration
- Atmospheric pressure changes
Manufacturers carefully design and test their packaging, shipping, and handling procedures to ensure the devices are protected from adverse conditions during transit.
The Impact of Proper Packaging on Medical Device Shelf Life
Proper packaging is critical to ensure the long-term stability and effectiveness of medical devices. It protects devices from environmental factors such as moisture, light, and oxygen, which can all contribute to device degradation and reduced efficacy over time.
Proper packaging is also critical for ensuring the safety and effectiveness of medical devices during transportation and storage. Proper packaging helps protect devices from adverse conditions encountered during transit and ensures that they arrive at their destination in the same condition as they left the manufacturing facility.
Similarly, proper storage of devices requires careful attention to packaging to prevent exposure to adverse environmental conditions that can shorten their shelf life.
Manufacturers carefully select the packaging of a medical device based on several factors, ensuring they provide the following characteristics:
- Barrier properties
- Chemical resistance
- Durability
- Impact resistance
- Temperature extremes
In these ways, proper packaging can extend the shelf life of medical devices and ensure that they remain sterile, functional, and safe for use.
Packaging That Meets Regulatory Requirements and Improves Shelf Life
Proper packaging is essential for ensuring the safe transport and storage of medical devices. With the right material, equipment, and techniques, you can ensure that your products have a longer shelf life and reach your customers in excellent condition. Proper packaging also ensures that medical devices are safe to use, which is critical for you and your patients.If you are in search of medical packaging that meets regulatory requirements and improves shelf life, Plastic Ingenuity has an excellent solution for you. As one of the largest custom thermoforming companies in North America, we create best-in-class thermoforming packages that prioritize safety and sustainability. Our innovative, scalable healthcare solutions empower you to get drug therapies, medical devices, and diagnostic products to the market faster. Contact us today to see how our custom end-to-end solutions and services can help ensure your project’s success.
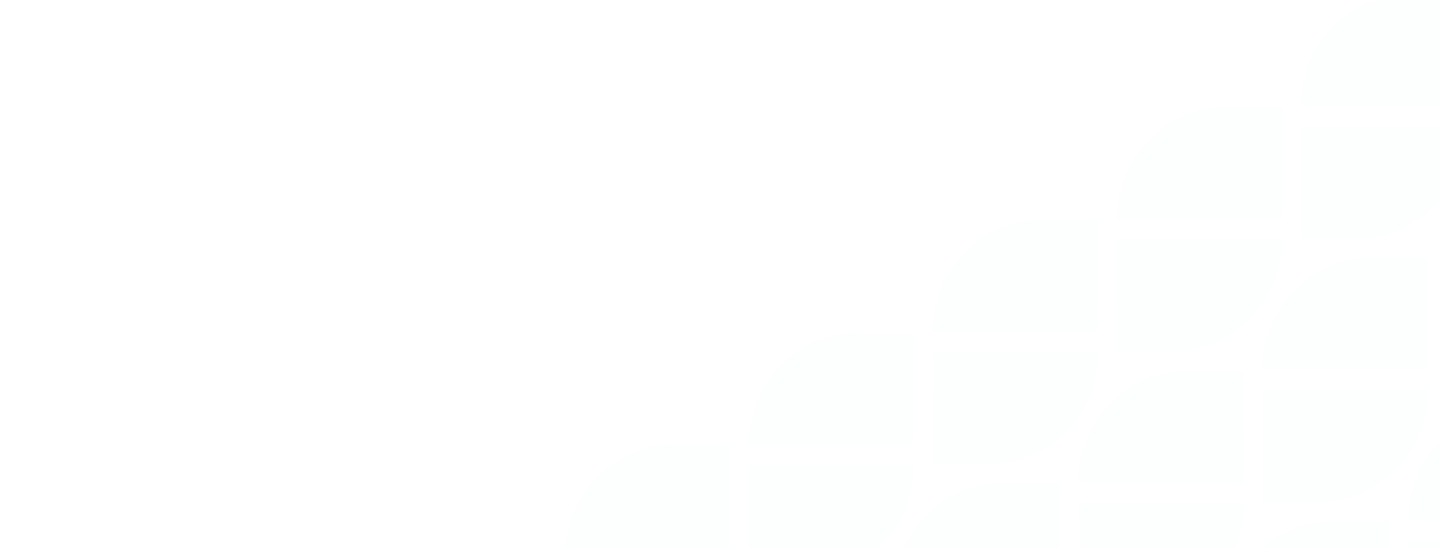