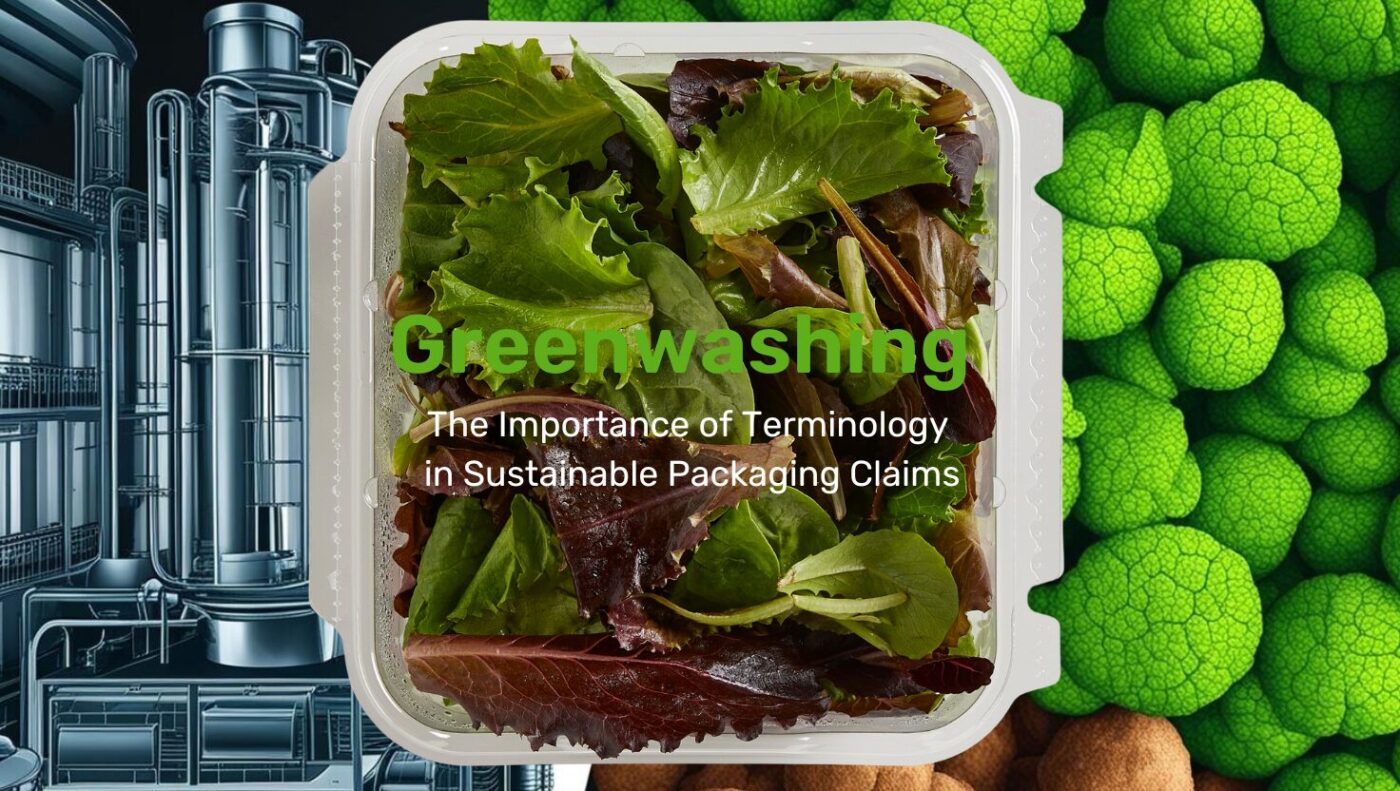
Understanding the Language of Sustainability As the push for sustainable packaging grows,…
Similar to the way a 3D printer works, co-extrusion is all about melting and reforming plastics. There are a number of different extrusion methods, but all work under generally the same principle. Here is a look at the way extrusion works and what makes co-extrusion unique.
In the extrusion process, a machine with a hopper collects plastic beads or pellets that are melded together into one product. Any additional coloring or protective substances that need to be included in the finished product are then added. From the hopper, the plastic is funneled into a temperature-controlled chamber or tube. This tube heats the plastic to the point of melting.
After the plastic is sufficiently melted, it may go through a variety of different molding processes. Plastic bags, plastic insulated wires, and PVC pipes are all created using an extrusion method. Common extrusion methods include:
Co-extrusion is defined by the number of plastic substances or polymers used in the extrusion process. The substances are heated separately and then joined together before being molded into the proper shape. Because some plastics aren’t as strong, durable, or weatherproof as others, using a combination of materials is the best way to meet the needs of a product specification. Common plastic bases include:
By combining plastics bases with different properties, packaging companies can create highly durable and effective packaging solutions for numerous applications. From dog toys to detergent bottles, the co-extrusion application is one of the most important aspects of the packaging manufacturing industry.