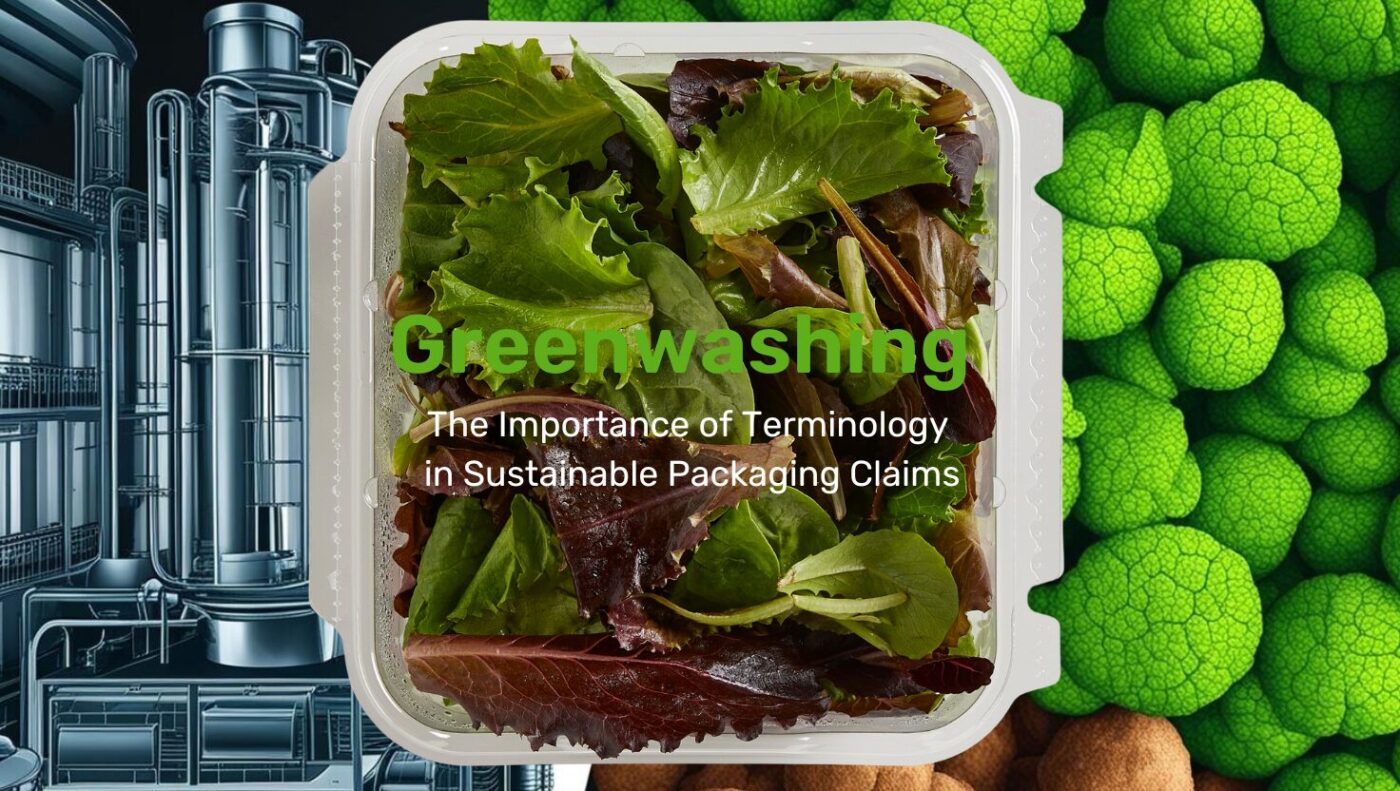
Understanding the Language of Sustainability As the push for sustainable packaging grows,…
Thermoforming is a popular manufacturing process that involves heating plastic sheets until they are pliable and then forming them into various shapes using a mold. This process is widely used in the packaging industry to create containers, trays, and other packaging products.
When it comes to thermoformed packages, companies have two main options: to do it in-house or to purchase it from a dedicated packaging supplier. In this blog, we’ll explore the pros and cons of in-house thermoforming to help you make an informed decision.
▪️ Greater process control – Having greater control over the design, manufacturing, and quality control processes can be beneficial for customers who have the most demanding quality and traceability requirements.
▪️ Increased manufacturing efficiency – Running in line with the rest of your manufacturing process can lead to options such as form, fill and seal, which can lead to increased manufacturing efficiency.
▪️ Lower freight and warehousing costs – It is more efficient to transport and store extruded sheet than formed parts, which can lead to cost savings for those sourcing over longer distances or requiring bulkier parts.
▪️ Faster turnarounds – thermoforming in-house shortens lead times and can lead to a more flexible process, which can be an advantage in industries with unpredictable demand fluctuations.
▪️ Large capital investment – There are significant startup costs related to in-house thermoforming. The cost of setting up a basic line with thermoforming, trimming, and quality control equipment (and associated infrastructure) may not be worth it for most operations.
▪️ Higher part prices – Counterintuitively, in-house thermoforming can lead to higher part prices. This is because a large, vertically integrated packaging supplier will extrude its own sheet from resin as opposed to buying roll stock – which leads to major cost savings. They can also grind and re-extrude all scrap generated from the trimming process, further reducing costs. Dedicated packaging suppliers have the economies of scale, purchasing power, and competitive pressure needed to provide the lowest prices possible.
▪️ Specialized training requirements – In-house thermoforming requires significant investments in ongoing training and developing expertise. The thermoforming process can be extremely sensitive to minute changes in material, temperatures, additives, etc. These issues require dedicated subject matter experts and state-of-the-art equipment to troubleshoot effectively.
▪️ Space constraints – Depending on the size of the operation, space constraints may be an issue. This is much more challenging than companies expect when warehousing plastic and other raw materials. If the in-house thermoforming operation is not designed to scale, capacity issues may arise, potentially limiting growth opportunities.
In summary – in-house thermoforming can be a good option for companies looking to run their thermoformers in line with the rest of their manufacturing process – especially if they benefit from having greater process control. However, it does come with significant additional costs and increased training requirements. Some of the benefits of in-house thermoforming (such as lower freight and warehousing costs) can be achieved by working with the right packaging supplier to set up satellite operations closer to your facility. Each project is unique and would likely have additional benefits and drawbacks beyond those listed here. If you would like more information on which model works better for you, please contact us. We would be happy to help!