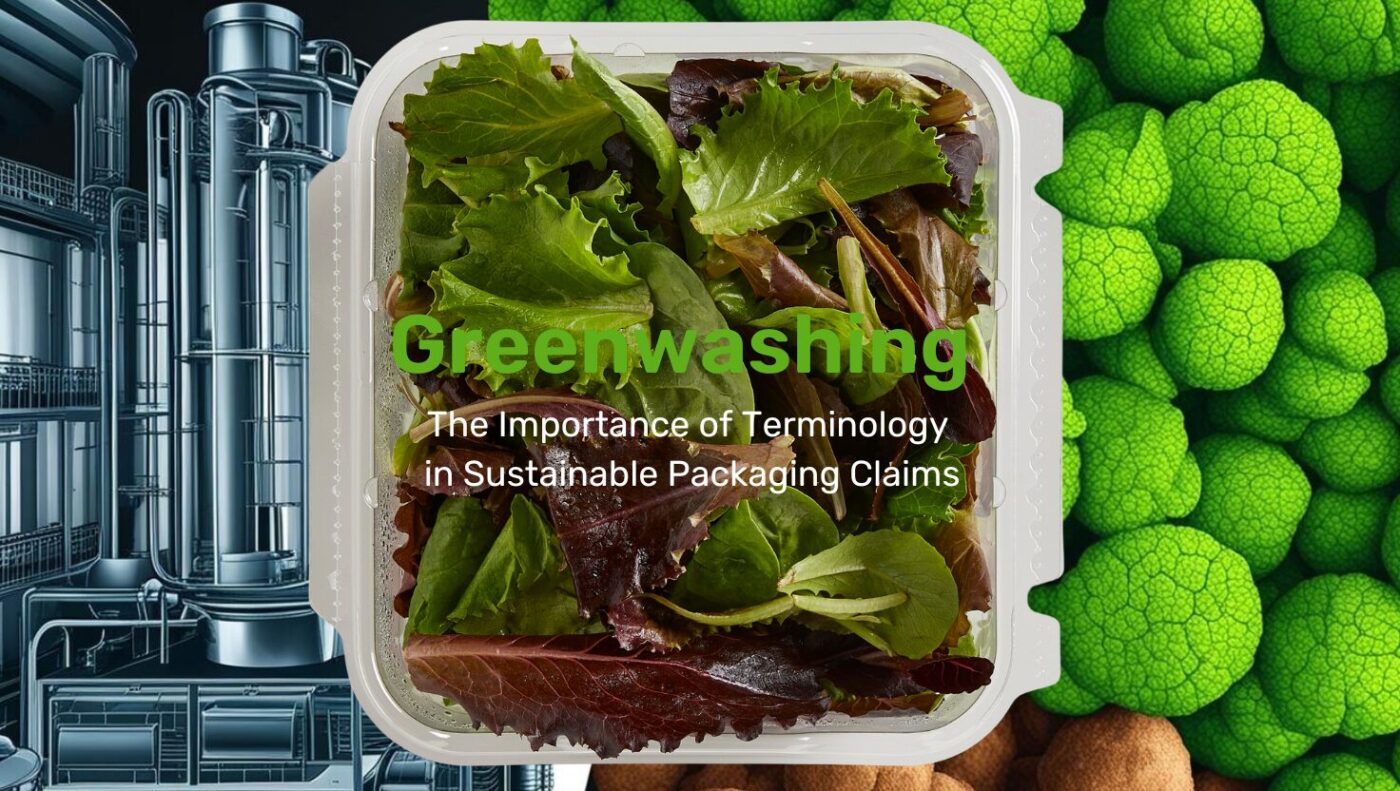
Understanding the Language of Sustainability As the push for sustainable packaging grows,…
The primary purpose of a package is to maintain product integrity, and intentional material selection is a critical component of a package’s success. PP is a popular packaging material for many applications due to its lightweight nature, extreme durability, and processing versatility. The customizable nature of PP allows this polymer to be produced in various colors and formats, such as thermoformed cups or trays, injection-molded containers, blow-molded bottles, and form-fill-seal packages. Due to these adaptable properties, PP is used across the food, beverage, cosmetic, household cleaning, and healthcare industries.
The widespread use of PP has led to challenges in recovery. Due to its diversity in size, format, and color, properly collecting and sorting PP has proven incredibly challenging compared to other commonly recycled materials. Unlike the PET water bottle or HDPE milk jug, PP does not have a distinguishable standard format to help with sortation. For decades, PP was sorted into mixed plastic bales, typically containing plastics 3 through 7 (PVC, LDPE, PP, PS, and others). These mixed plastic bales were commonly exported overseas until China’s National Sword policy in 2018 redirected the attention back to domestic markets for PP.
The Sustainable Packaging Coalition reported in their 2020–2021 Centralized Study on Availability of Recycling that PP tubs and containers had fallen to a 59% acceptance rate for recycling nationwide. According to the Association of Plastic Recyclers’ definition of recyclable, at least 60% of consumers must have access to a collection system that accepts the item per the FTC Green Guides. Therefore, PP tubs and containers were downgraded to a “check-locally” status by SPC’s How2Recycle program. This distinction catalyzed The Recycling Partnership’s Polypropylene Recycling Coalition in July 2020. Plastic Ingenuity joined TRP’s Polypropylene Recycling Coalition in August 2021.
Since the Coalition’s birth, industry leaders reinforced PP’s value as a recycled material and its essential role in the circular economy. Significant investments by TRP’s Polypropylene Recycling Coalition to improve PP recovery in the U.S. included grants impacting 600 communities and 41 material recovery facilities (MRFs).
In early 2022, the Sustainable Packaging Coalition and The Recycling Partnership worked together to evaluate access rates and end-market criteria for PP. By leveraging TRP’s National Recycling Database and Circular Packaging Assessment tool, the evaluation proved that polypropylene’s access rate increased to 65% and demonstrated growth in domestic end markets. This collaborative evaluation by SPC and TRP returned most PP applications to a “widely recyclable” designation by How2Recycle.
The Recycling Partnership estimates that single-family households in the U.S. generate more than 2 billion pounds of polypropylene annually. If MRFs recovered 30% of this material, it would provide over 600 million pounds of recycled material and reduce greenhouse gas emissions by 311,000 metric tons of CO2.
The investments in curbside access and MRF investments by TRP’s Polypropylene Recycling Coalition truly make a difference. A compelling example of the Coalition’s success can be found in the state of Ohio. At the close of 2020, a mere 34% of Ohio households had access to recycle polypropylene. Thanks to the Coalition’s grant initiatives, this figure has impressively surged to 69%, demonstrating the tangible impact of their concerted efforts. Rumpke Waste & Recycling, with MRFs in Columbus and Cincinnati, received an MRF grant from TRP. As a result of these investments, more than 1 million new pounds of PP is recovered per year in this area.
Although PP is the third-highest material by volume in a residential recycling bin, behind PET and HDPE, sortation capabilities for PP are underdeveloped compared to PET and HDPE. However, significant improvements in sortation technologies have increased efficiency and stream acceptance for PP.
Optical Sorters
Optical identification through near-infrared (NIR) scanning technology is increasingly prevalent in MRFs. This technology uses sensors and cameras to identify and sort recyclables based on their material properties. Optical sorters are being strategically applied to identify and sort PP into its own bale.
Robotics
Robotic arms built over conveyor belts aim to enhance the automatic sorting process at a MRF. Robots are capable of 40–100 picks per minute, drastically increasing efficiency and reducing manual labor.
Artificial Intelligence
AI technology is designed to be used with optical and robotic sorters to increase the number of easily identified and sorted materials. Cameras capture images of the waste stream across a conveyor belt while AI algorithms simultaneously analyze the pictures for visual characteristics such as the shape and color of materials.
The demand for recycled polypropylene (rPP) continues to grow as 2025 brand commitments for recycled content are just over the horizon. An increased supply of rPP will require growing collection through policy changes such as extended producer responsibility (EPR), improvements in sorting capabilities for PP-only bales, and a growing capacity for food-grade rPP.
Food grade rPP production presents challenges due to its various grades, colors, and formats. Not all PP grades are food-grade, so creating a clean stream of food-grade rPP has proven difficult. Because of PP’s ability to absorb chemicals when used for non-food purposes, rPP feedstocks must undergo extensive source control and decontamination to be considered food-grade. However, a small number of reclaimers, including KW Plastics, Plastic Recycling Inc., Envision Plastics, Merlin Plastics, and PureCycle, have received a letter of no objection (LNO) for food contact rPP from the FDA. The FDA LNO approval is based on the process developed by the reclaimers to produce food-grade material, including a complete description of the recycling process, passing results of surrogate contaminant challenge testing, and the intended conditions of use for the material.
An FDA LNO is becoming ever more prevalent as demand for rPP increases. Plastic Ingenuity is uniquely positioned within the value chain to evaluate food-grade rPP options from reclaimers. We also provide brands with support and guidance as they incorporate rPP into their packaging systems to meet recycled content goals.
PP’s widespread use in packaging has led to an increase in PP generated by U.S. households and a surge in demand for post-consumer recycled PP. Although there is still work to be done to increase recycling rates, improve sortation capabilities, and increase the supply of food-grade material, the signs of change for PP recovery are encouraging.
While polypropylene recycling has made significant strides with the support of The Recycling Partnership’s PP Recycling Coalition, plenty of work remains to unlock the full spectrum of environmental and economic benefits associated with PP recycling. PP recycling holds a promising future and, with continued support and investment, it is well on its way to contributing to a more sustainable and circular economy.