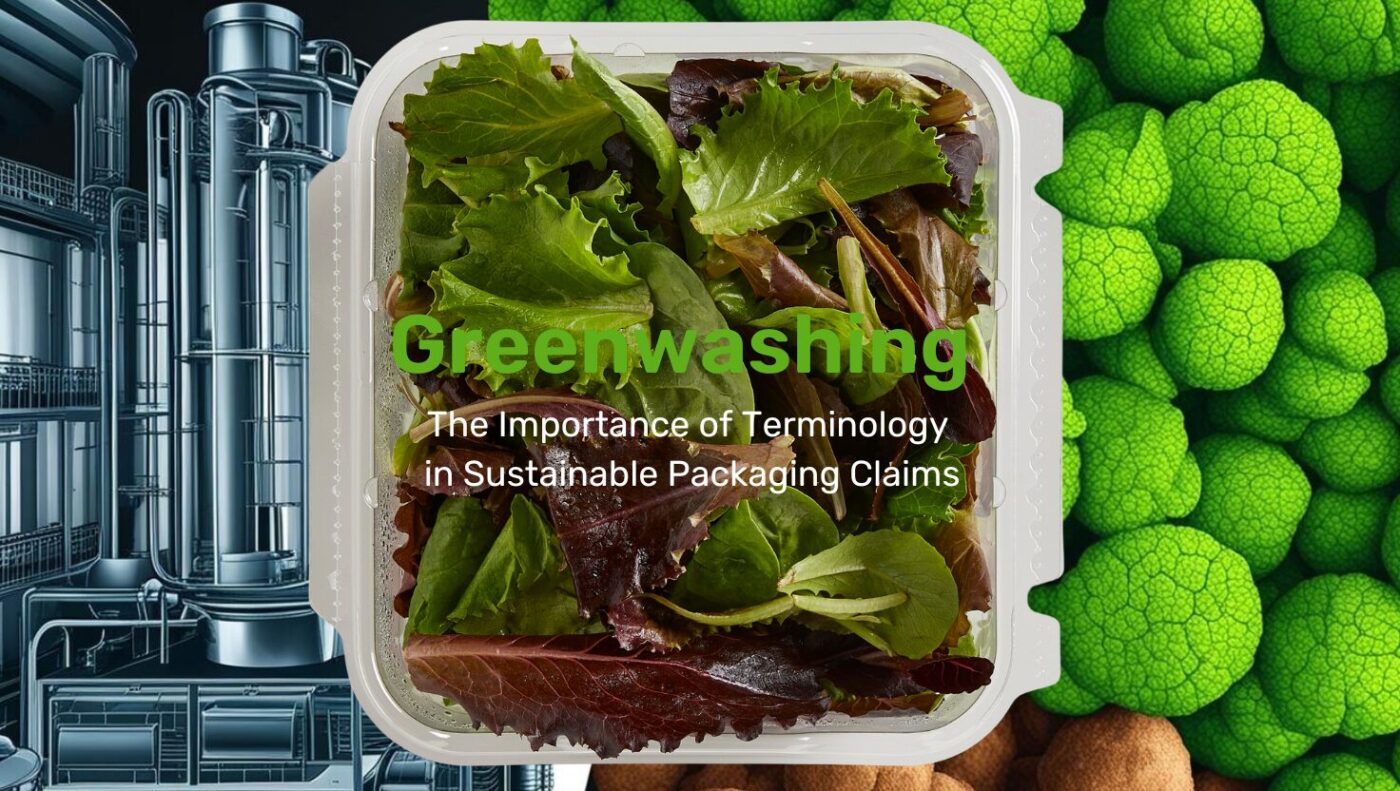
Understanding the Language of Sustainability As the push for sustainable packaging grows,…
Medical device packaging requirements in the U.S. are rigorous. And it makes sense, given that patient health and safety are at stake. The FDA’s Center for Devices and Radiological Health (CDRH) institutes comprehensive regulations for medical device packaging that all device manufacturers, repackagers, and importers must adhere to.
These medical device packaging requirements by the FDA govern all aspects of device packaging, including labelling, sterilization, and package materials. You must know and strictly follow these regulations in your supply chain and manufacturing process.
You must also adhere to additional requirements per your FDA medical device classification and other standards from pertinent authorities such as the European Medicines Agency. More importantly, your packaging design must facilitate ease of access for all device users, whether they’re self-administering individuals or professionals in healthcare facilities.
Let’s discuss the six most crucial packaging requirements you must implement.
Even before you satisfy packaging requirements, you should establish your medical device classification (Class I, II, or III). This helps you understand the specific regulatory provisions governing your packaging standards and marketing practices.
For instance, if your device is classified under Class III, you must submit a Premarket Notification 510(k) before being allowed to distribute your device commercially. In such a case, class I medical device packaging requirements may not suffice for your Class III device.
When you’ve classified your medical device, you may now cater to these six packaging requirements:
The Code of Federal Regulations Title 21 defines labelling as “all written, printed, or graphic matter accompanying an article at any time while such article is in interstate commerce or held for sale after shipment or delivery in interstate commerce.”
This means that any printed material on your medical device, the device’s wrapper, and other messaging/marketing material, such as tags and pamphlets, qualify as labels. Your label must satisfy FDA’s general labeling requirements for medical devices. This provision states that FDA-compliant labels must include:
You must also know the practices that count as mislabelling. These include:
The quality of raw materials can directly influence your medical device’s efficiency and overall safety. There are many raw materials that medical device companies can use for packaging. They include
To ascertain the quality of your raw material and if it’s the best fit for your medical device, conduct raw material characterization screening. This screening helps you:
Raw material testing enables you to establish a quality standard for each material. You then apply this standard to qualify new suppliers, benchmark the quality of new raw materials, and as a reference when reviewing the quality of a suspicious batch of material.
Single-use sterile medical products have gained popularity in the medical field as they have reduced the costs and risks of in-hospital sterilization. Fortunately, sterile barrier systems (SBS) ensure your sterile medical devices maintain sterility up to the point of use.
SBS prevents contamination from microorganisms by creating a microbial barrier during packing and facilitating the aseptic presentation of your product until the end consumer uses it. Overall, these are the three types of SBS as defined in ISO 11607:
To maintain their sterile condition, you must ensure sterile medical devices remain sealed until the end users open the package. This means the seal must have enough strength to endure all the shipping stresses, such as vibration, shock, and temperature changes that devices may experience throughout the logistics cycle.
That’s why you must conduct seal strength testing to assess the seal properties of your package. You can test your package for seal leaks through:
Package integrity testing seeks to identify any packaging defect that can significantly dilute the sterility of a medical device. It’s part of FDA requirements for medical device shelf life and packaging testing. Operational qualification tests are most suitable for accessing package integrity. They include:
Additionally, stability testing requirements for medical device packaging identify how sturdy a package is when subjected to different environmental conditions such as gravity, pH, temperature, agitation, moisture, and light.
Sustainability is a frontline priority for all industries across the board. Medical device companies can promote sustainability by adopting environmental-friendly disposal practices and packaging materials and still utilize their preferred custom packaging options.
You can also optimize your packaging systems to reduce package weight and size — for instance, by using single sterile-barrier packaging instead of dual sterile-barrier packaging.
To manufacture bespoke custom-made devices, you need top-notch packaging systems, an eye for design, and strict adherence to the evolving medical device packaging requirements. This can be a lot on your plate, especially if you’re a prominent or upcoming medical device manufacturer.
But if you partner with a company dedicated to improving healthcare, you’ll be in a better position to fulfill packaging requirements with little hassle. Partnering with Plastic Ingenuity is strategic, especially if you’re scaling fast or want to expedite your packaging processes.
We know firsthand the importance of your raw material input and how critical your supply chain is. That’s why we source and utilize materials that are certified to meet FDA & EU MDR ROHS, BSE/TSE, and virgin resin properties. On top of all, we follow GMP and ISO requirements during our sourcing and manufacturing processes.