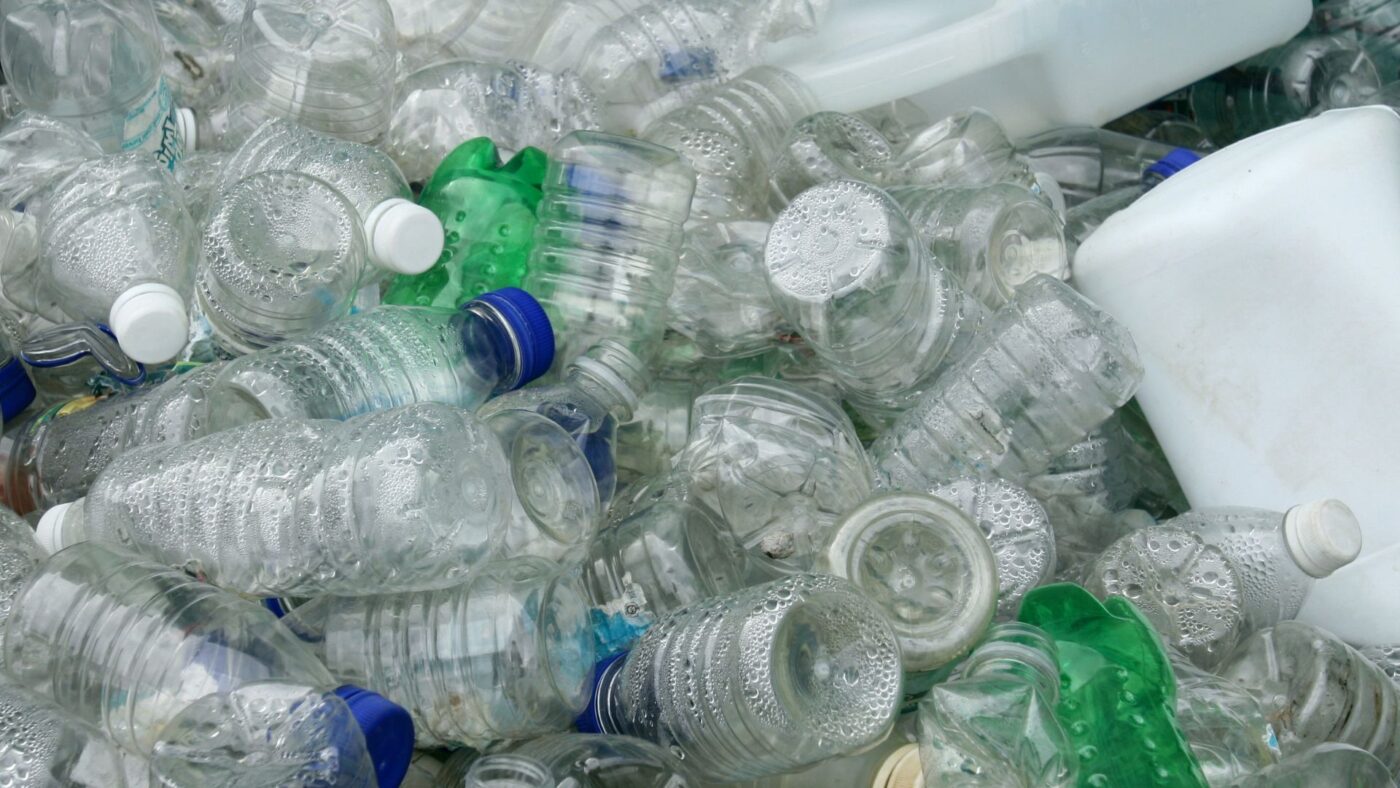
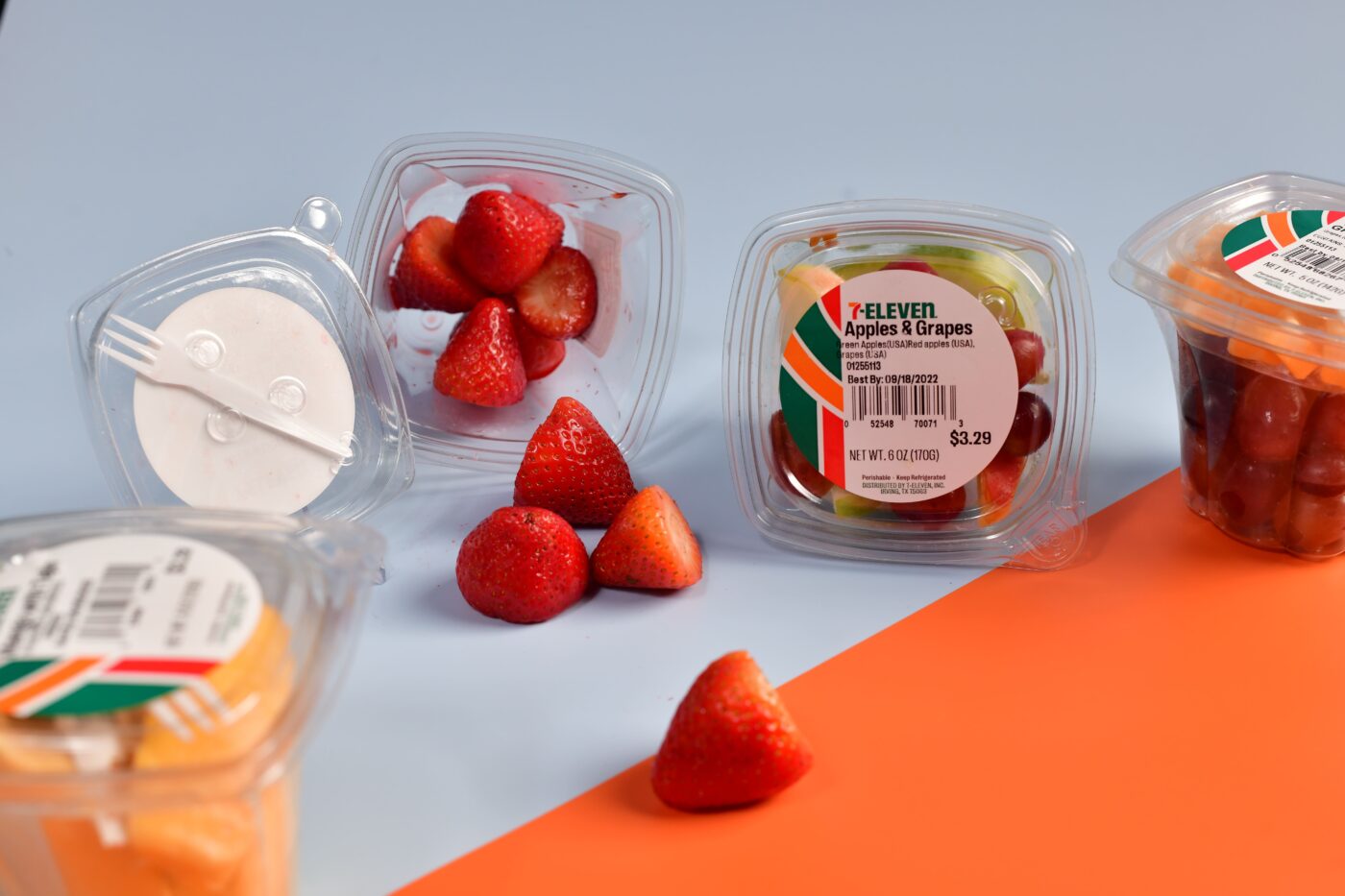
Get the Details
Facts About Thermoforms:
Thermoforms have immense utility across a variety of applications. When you think about it, thermoforms can be found at many touchpoints throughout your day. From playing an essential role in preserving the food we serve to protecting the medical devices we trust. Given thermoforms lightweight nature and relatively low energy to produce and transport, they have lower greenhouse gas emissions per package than alternatives. When you factor in preservation attributes, such as extending the useful life of perishable foods, thermoformed packaging offers significant benefits to society. But the problem remains; we need solutions that keep thermoforms out of landfills so we can continue to reap their benefits.
We’re a plastics company –always will be –but we are on a mission to improve the end-of-life outcomes for the thermoformed plastics we make. As active members of targeted associations highlighted below, we’ll continue to dedicate the resources needed to collaborate, learn, grow, and succeed.
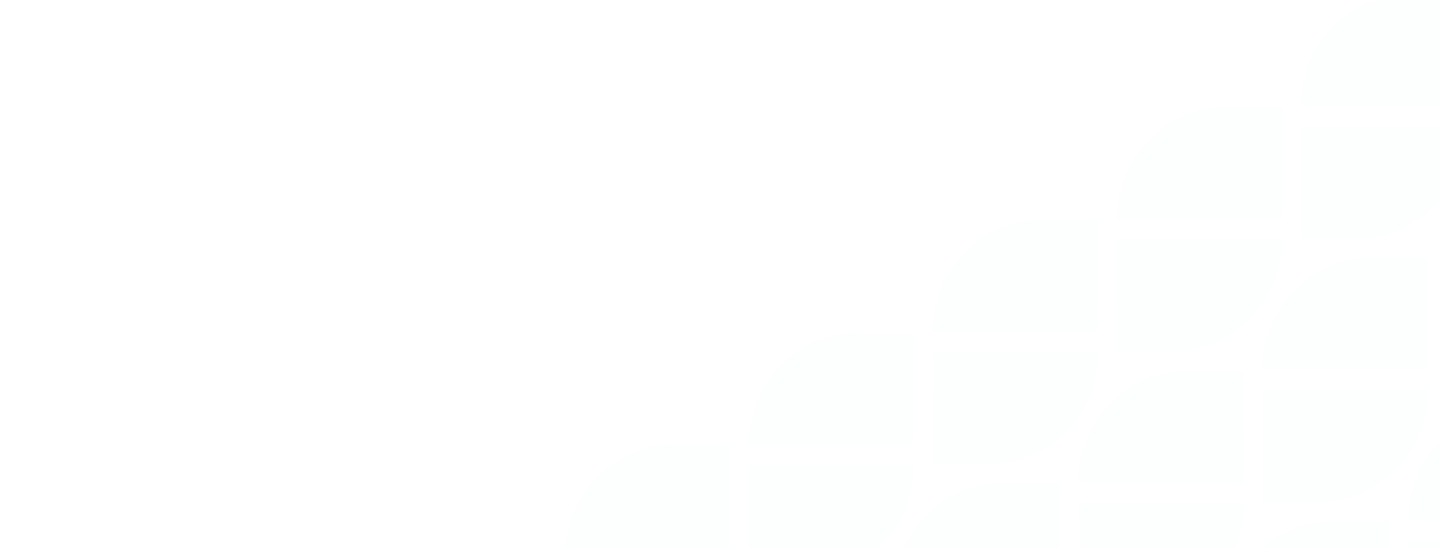
What is Plastic Ingenuity’s process to help me reach our goals?
Part of our circularity goals not only include what Plastic Ingenuity can do but also how we can help those we serve. Through innovation, education, and influence, we work with our customers to reach their internal circularity goals, offering a range of services tailored to each customer.
Here’s how we get things done.
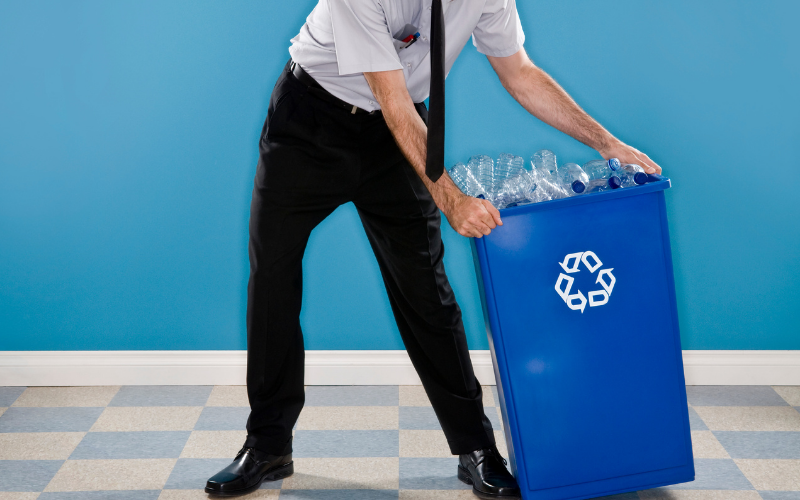
First, our dedicated team works with you to identify and refine your sustainability packaging goals.
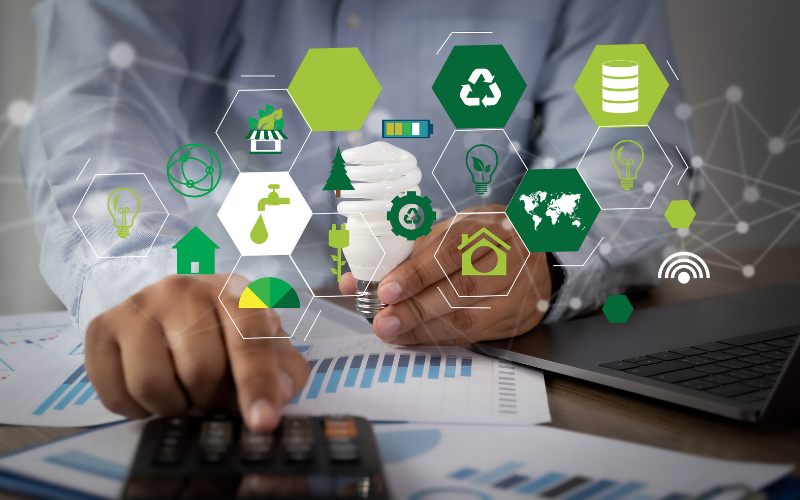
Then, we create a Sustainable Packaging Assessment. We discuss design and material choices, analyzing the impact different options have on the environment. Since we’re active members in the Association of Plastic Recyclers (APR), we’ve engrained design for recycling principles into our package development process.
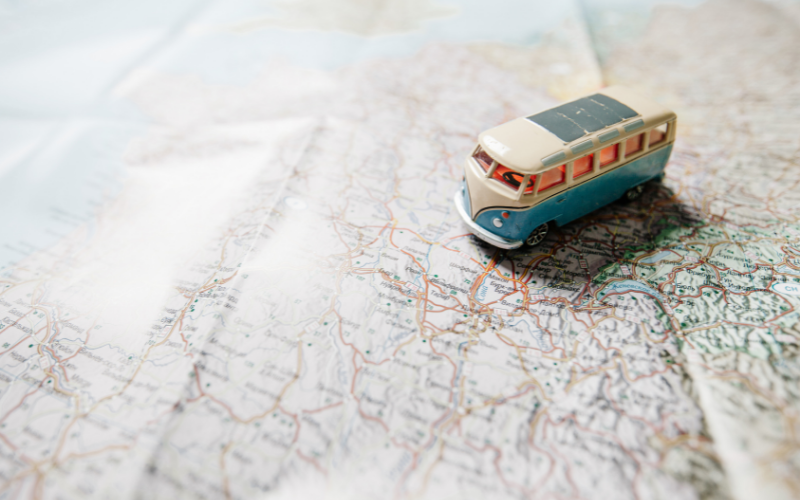
Next, we create a roadmap of where you are now, where you want to be and all the steps in between. This intricate plan creates a path to execute actionable results.
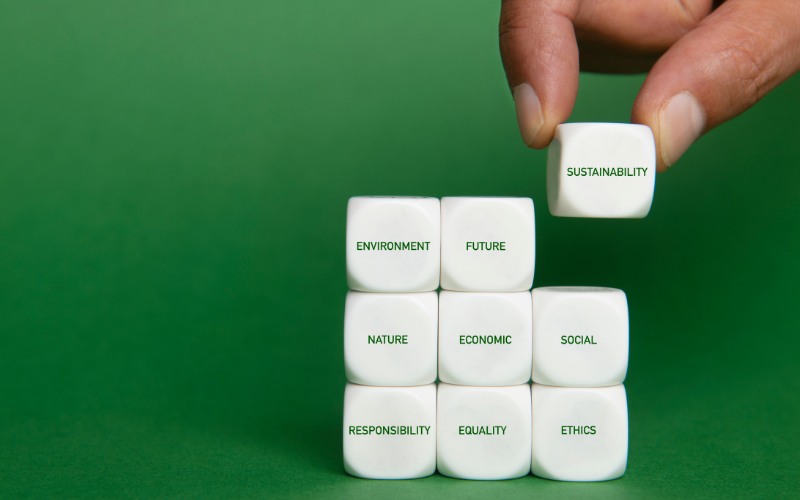
Last – and this is where we shine – we deliver. Your product, our skills, and shared passion of circularity, allows us to produce your final product. We control the entire process from design, extrusion, to delivery, and everything in between, allowing us to achieve our shared goals. If this is a process that sounds beneficial to you, find a few more details here.
Are there examples of this process in action that has shown success?
Glad you asked. We strongly believe that true circularity cannot be achieved without including thermoforms. Our mission as a responsible packaging producer is to create circular solutions that keep thermoforms out of landfills and out of our environment. Here’s a couple examples of how we have worked with our customers to reach their circularity goals.
-
Food Packaging
The Goal: Incorporate 80% PCR into an existing food tray
The Process: We dove in and conducted a sustainability assessment focusing on material efficiency, structure selection, and design for recovery. Then, we drafted a sustainability improvement road map in collaboration with Creminelli to determine the best path forward. We conducted trials and tests to ensure performance.
The Result: Our engineering experts determined the trays could be downgauged to reduce material usage without compromising performance. Additionally, we also purposed the use of post-consumer recycled content in the tray to improve the circularity.
The Impact:
80% PCR Content = 11,284,180 recycled water bottles
6 metric tons of greenhouse gas emissions reduced
7% reduction in material useFor specifics, please click click here.
-
Healthcare Packaging
The Goal: Eliminate shipping damage, decrease material waste, and reduce packaging costs.
The Process: We needed to develop a delicate, protective, bulk work-in-process solution. We leveraged Eastalite™ copolyester, a novel foamed PETG material. From there, we designed a 5-cavity, bulk universal tray to meet the project requirements.
The Result: The universal cavity design prevented device vibration and movement, improving the product protection with zero rejects in a bulk pack solution.
The Impact:
57% reduction in transatlantic freight costs
52% reduction in packaging material costs
133% increase in devices per palletTo learn more about this project, please click here.
-
Consumer Goods Packaging
The Goal: To move their packaging material from PVC to PET – a contaminate in the PET recycling system.
The Process: We worked with Wahl Clipper Corporation to identify potential PVC alternatives. The PI engineers evaluated performance requirements for each tray. After a series of testing, PET was selected.
The Result: All packages were converted to PET, and are now more recyclable, as durable and meet NGO and key retailer goals.
The Impact:
5,000 samples were produced
25 parts were transitioned to PET
102,000 pounds transformed from PVC to PET annuallyLearn more here.
Alignment with the U.N. Sustainable Development Goals.
The United Nations Sustainable Development Goals (UNSDGs) provide a framework for organizations and governments to follow to ensure the development of new goods and services are as sustainable as possible. This is a holistic, people-centered approach with categories ranging from “no poverty” to “peace and justice”. Plastic Ingenuity is committed to aligning with the UNSDG framework. The following information details our alignment and progress to date.
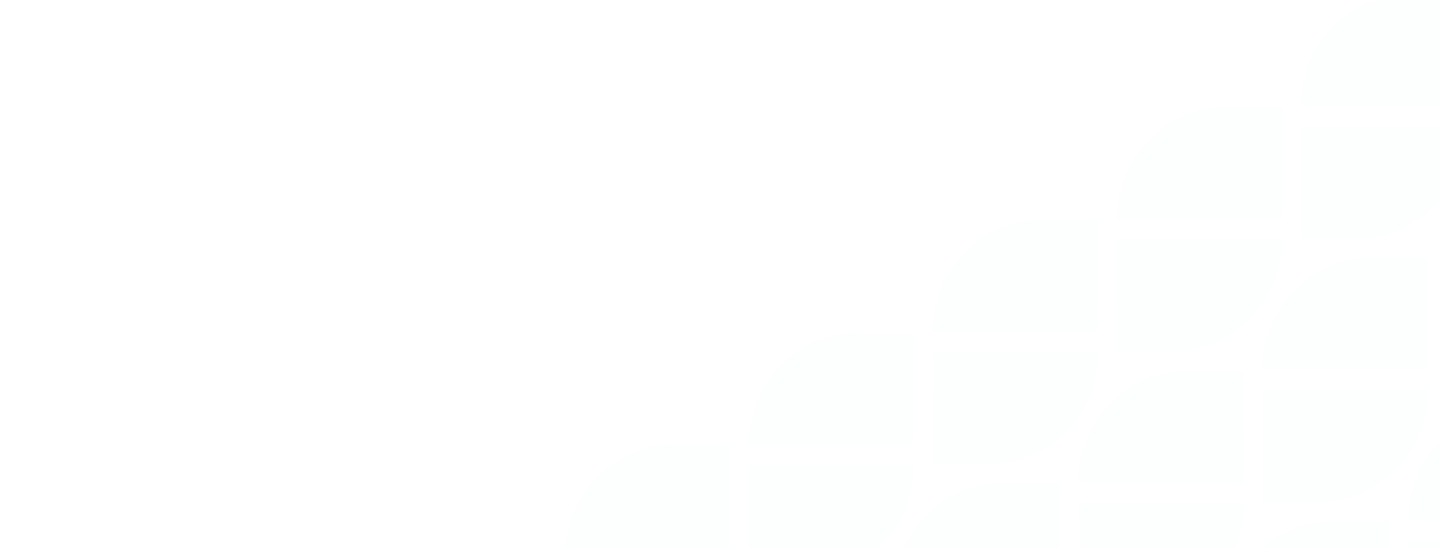
Memberships & Committees
PLASTICS (Plastics Industry Association), serving on the recycling committee | Recycling Partnership, partner member | PP Recycling Coalition, funding member | Association of Plastics Recyclers, proud member | Sustainable Packaging Coalition, proud member | NAPCOR (National Association for PET Container Resources), serving on the Board of Directors and Chair of the Thermoforming Committee | Foodservice Packaging Institute, proud member | Healthcare Plastics Recycling Council, proud member | Associated Recyclers of Wisconsin, proud member
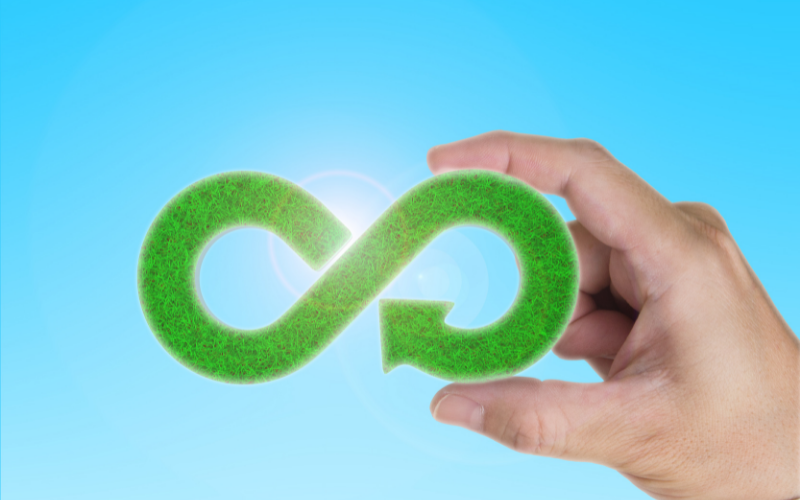
Let's get started
So, what's next?
As packaging professionals passionate about developing more circular packaging, there’s a lot outside of our control. Honestly, it can be frustrating at times. By focusing on the positives, solutions are available today using readily available technology and well-established best practices. Increasing the circularity of all packaging types will require an unprecedented level of collaboration. The challenges we face as a packaging industry are too steep to face alone. We must work together to make the progress that is rightfully expected of us. We’re proud of the steps we have taken, but this is just the beginning.
However, we’re up for the challenge. Are you?
When you’re ready to discuss more, we’d love to connect you with our Sustainability Team to discuss the impact a circular approach could have your product – and the environment.
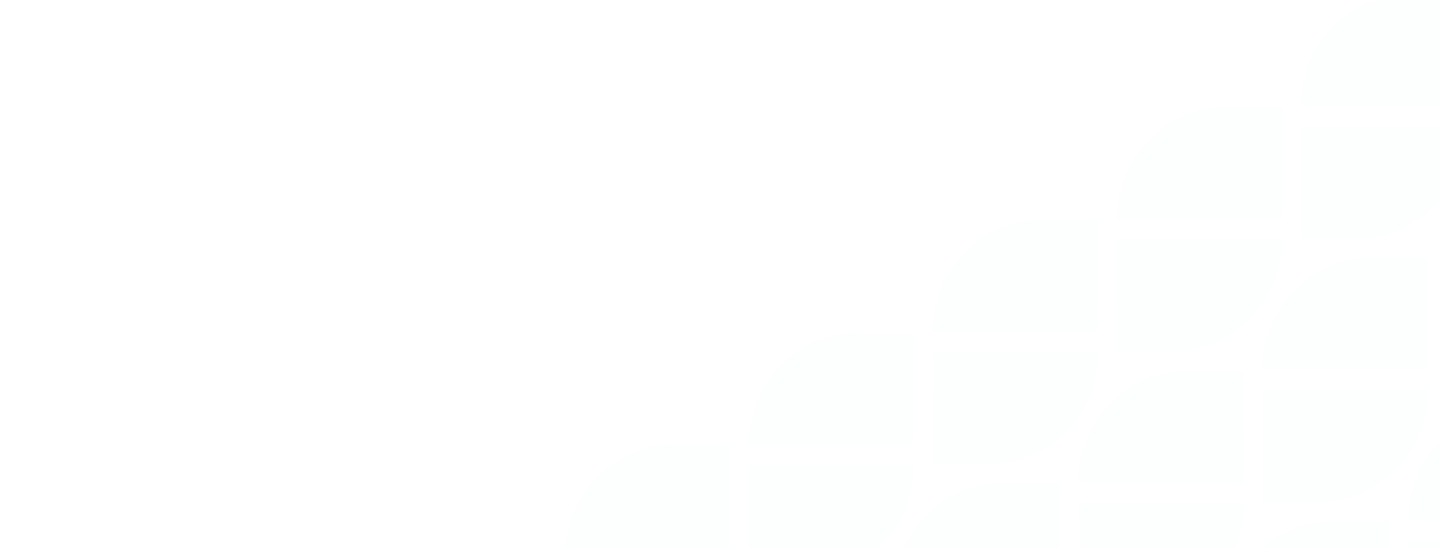